Alcast Company - An Overview
Alcast Company - An Overview
Blog Article
Unknown Facts About Alcast Company
Table of ContentsAll About Alcast CompanyThe Of Alcast Company3 Simple Techniques For Alcast Company6 Simple Techniques For Alcast CompanyThe Basic Principles Of Alcast Company How Alcast Company can Save You Time, Stress, and Money.
The refined difference hinges on the chemical material. Chemical Comparison of Cast Aluminum Alloys Silicon promotes castability by reducing the alloy's melting temperature and enhancing fluidness during casting. It plays a critical role in enabling complex mold and mildews to be filled precisely. In addition, silicon adds to the alloy's stamina and put on resistance, making it valuable in applications where sturdiness is critical, such as auto parts and engine parts.It additionally enhances the machinability of the alloy, making it much easier to process right into finished products. In this method, iron adds to the general workability of aluminum alloys.
Manganese contributes to the toughness of aluminum alloys and enhances workability. Magnesium is a light-weight component that gives strength and influence resistance to light weight aluminum alloys.
Indicators on Alcast Company You Need To Know
It permits the manufacturing of light-weight parts with excellent mechanical properties. Zinc improves the castability of aluminum alloys and aids regulate the solidification procedure during spreading. It enhances the alloy's strength and solidity. It is commonly found in applications where complex shapes and fine details are essential, such as attractive spreadings and certain auto components.

The main thermal conductivity, tensile toughness, return toughness, and prolongation differ. Amongst the above alloys, A356 has the greatest thermal conductivity, and A380 and ADC12 have the least expensive.
All About Alcast Company
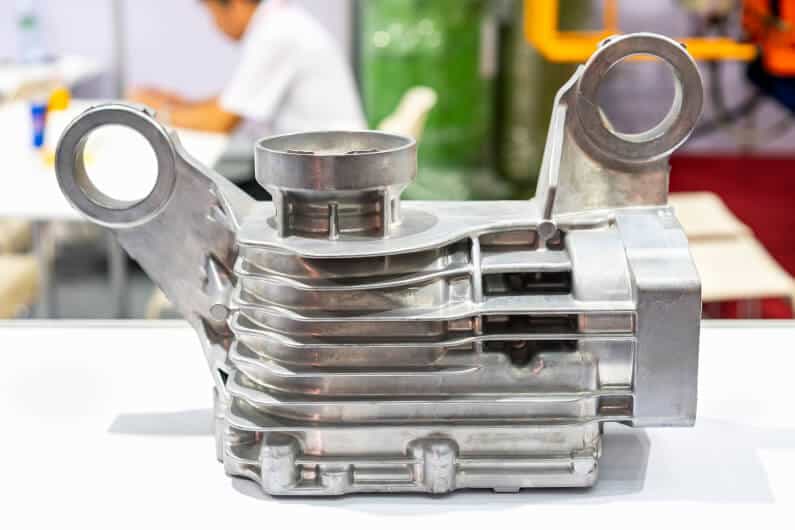
Its special residential properties make A360 a useful option for accuracy spreading in these markets, improving item toughness and top quality. Light weight aluminum alloy 380, or A380, is a commonly made use of check these guys out spreading alloy with numerous unique attributes. It supplies outstanding castability, making it an optimal option for accuracy spreading. A380 displays good fluidness when molten, making sure elaborate and thorough molds are precisely reproduced.
In accuracy spreading, aluminum 413 radiates in the Consumer Electronic Devices and Power Devices sectors. This alloy's premium rust resistance makes it an excellent choice for outside applications, guaranteeing durable, sturdy products in the mentioned industries.
Fascination About Alcast Company
When you have actually chosen that the aluminum pass away casting process appropriates for your task, a critical following action is selecting the most ideal alloy. The aluminum alloy you pick will significantly affect both the casting process and the properties of the end product. Since of this, you must make your choice thoroughly and take an educated method.
Determining the most ideal light weight aluminum alloy for your application will mean evaluating a large selection of characteristics. The very first group addresses alloy features that influence the production procedure.
Alcast Company Things To Know Before You Buy
The alloy you choose for die spreading directly impacts a number of aspects of the casting process, like exactly how easy the alloy is to deal with and if it is prone to casting issues. Hot breaking, additionally referred to as solidification cracking, is a common die casting problem for aluminum alloys that can cause inner or surface-level tears or fractures.
Certain light weight aluminum alloys are much more susceptible to warm breaking than others, and your selection should consider this. It can damage both the actors and the die, so you need to look for alloys with high anti-soldering buildings.
Corrosion resistance, which is currently a remarkable attribute of light weight aluminum, can vary significantly from alloy to alloy and is an essential characteristic to think about depending upon the ecological problems your product will certainly be subjected to (Aluminum Casting). Use resistance is an additional home generally looked for in light weight aluminum items and can distinguish some alloys
Report this page